Additive Manufacturing: A Paradigm Shift
- Lothric Labs
- Apr 13, 2024
- 2 min read
Updated: Sep 18, 2024
Additive manufacturing revolutionizes the way products are designed, prototyped, and manufactured. Unlike traditional subtractive methods that involve cutting away material from a solid block, AM builds objects layer by layer. This process enables unprecedented design flexibility and customization, making it a game-changer in various industries.
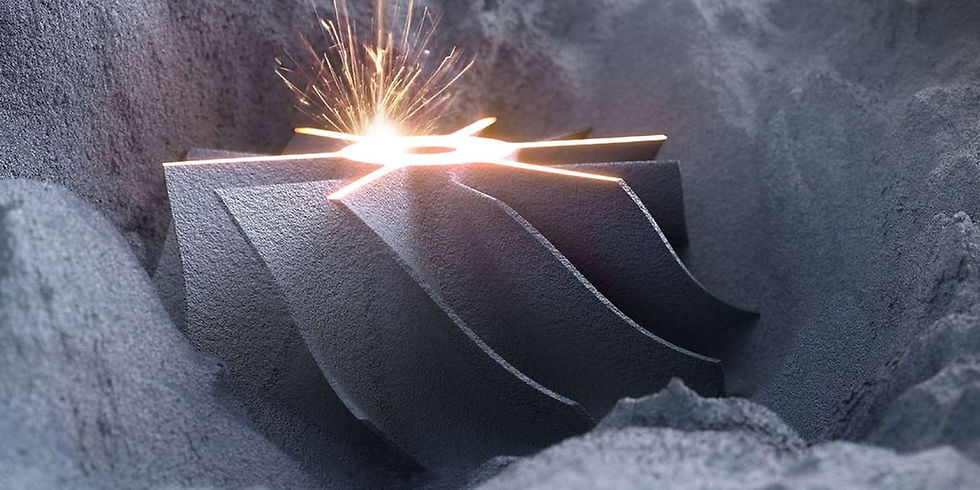
The Four Pillars of Additive Manufacturing Value
Design Freedom and Performance Enhancement:
AM technologies allow designers to create parts with almost any 3D shape. This freedom enables the development of components that perform better or cost less than conventional alternatives.
For instance, Airbus produced an additively manufactured titanium bracket that is 30 percent lighter than its predecessor without compromising performance or durability.
Mass-Scale Customization:
Traditional manufacturing relies on molds and fixed tooling, limiting customization. In contrast, AM produces each part uniquely.
Test equipment maker Vectoflow leverages AM to create bespoke probes for fluid flow measurement. These compact and complex designs minimize impact on the flows being measured.
Accelerated Product Development and Production:
AM eliminates time-consuming toolmaking and fabrication operations. As a result, product development and production cycles shorten significantly.
The Ariane 6 rocket’s complex fuel injector head is now additively manufactured as a single piece of nickel-based alloy. Previously, it required welding together 248 individually machined components.
On-Demand Maintenance and Spare Parts:
AM simplifies maintenance by enabling on-demand production of items from digital files. Spare parts can be created when needed, reducing the need for large inventories.
Carmaker Mercedes-Benz uses AM to produce spare parts for its classic vehicles.

From Prototyping to Production
Initially, AM was primarily used for functional prototypes during product development and testing. It allowed inventors and engineers to quickly create physical parts based on digital designs.
However, the landscape has evolved. AM technologies are now applied in a growing range of indirect applications, including:
Tooling: AM-produced tools enhance efficiency in conventional manufacturing.
Spare Parts: On-demand production reduces spare-parts inventories.
Fixtures: AM fixtures support conventional manufacturing machines.
The Race Ahead
As of 2020, the AM sector had grown into a €13.4 billion industry with a 22 percent annual growth rate.
Over 200 players compete to develop new hardware, software, and materials.
Rapid innovation is overcoming perceived limitations, such as overhanging parts without elaborate support structures and controlled alignment of fiber reinforcements using magnetic fields.
In summary, additive manufacturing has moved beyond prototyping to support production at scale. Its impact on manufacturing is profound, and businesses must embrace this transformative technology to stay competitive in the modern era123.
Remember, the future is now, and 3D printing is no longer just science fiction—it’s our reality! 🚀🔍